What is an Incremental Encoder Quadrature?
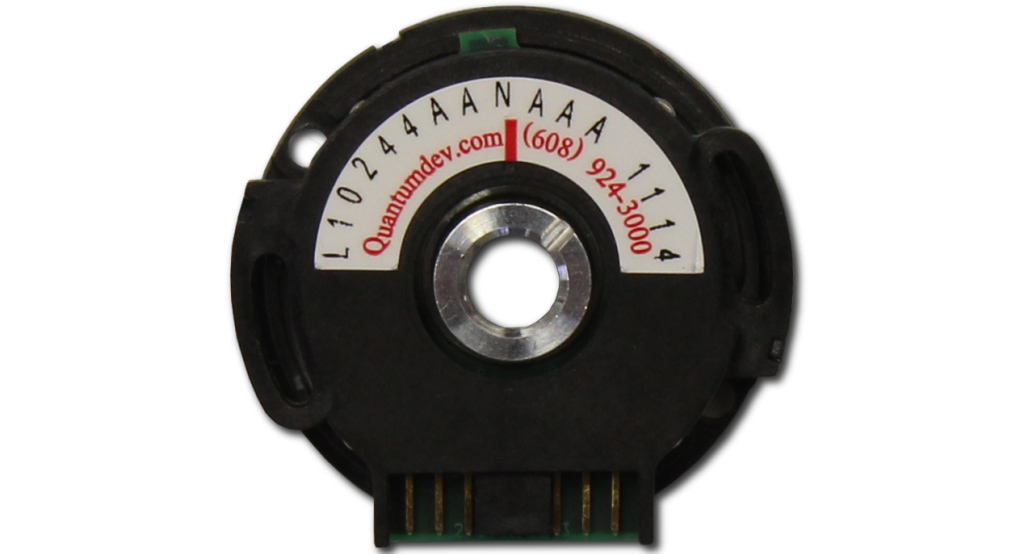
An incremental encoder is a position sensor that provides relative motion information about a rotating shaft. It produces two output signals, typically A and B channels, that change state as the shaft rotates. The quadrature feature of the encoder means that the two signals are out of phase by 90 degrees or a quarter of the cycle. The encoder resolution or the number of pulses per revolution is determined by the number of lines or slots on the encoder disk or strip.
The A and B channels of the quadrature encoder produce a unique pattern of pulses, also known as the quadrature state, that allows the decoder or the receiving device to determine the direction and speed of the shaft. By monitoring the relative phase shifts and pulse counts of the A and B channels, the encoder can provide precise measurements of the rotational position, velocity, frequency, and acceleration of the machinery.
Features and Benefits of Incremental Encoder Quadrature
The incremental encoder with quadrature outputs offers several advantages over other types of encoders, such as absolute encoders or digital tachometers. Here are some of the features and benefits of incremental encoder quadrature:
- High Accuracy: Quadrature encoders provide high resolution and repeatability, with resolutions up to 10,000 pulses per revolution or more. This means that the encoder can detect even the smallest changes in the shaft position or speed, making it suitable for applications that require precise motion control or feedback.
- Bi-Directional Output: The quadrature outputs of the encoder allow the decoder to determine the direction of the shaft, whether it is rotating clockwise or counterclockwise. This feature is useful in applications where the shaft needs to be reversed or stopped quickly, such as in motor control or robotics.
- Real-Time Feedback: The incremental encoder quadrature provides real-time feedback about the motion of the machinery, enabling the controller or the operator to adjust the speed, position, or acceleration accordingly. This feature is critical in applications that require smooth and accurate motion, such as CNC machines or robotics.
- Compact and Durable: Most incremental encoder quadrature devices are compact and lightweight, making them suitable for space-constrained environments or mobile applications. Furthermore, they are designed to operate in harsh industrial environments, with rugged and corrosion-resistant materials, such as stainless steel or aluminum.
Applications of Incremental Encoder Quadrature
The incremental encoder quadrature is widely used in various industries that require precise motion control and measurement. Here are some examples of applications where incremental encoder quadrature is commonly used:
- Industrial Automation: In industrial automation, the incremental encoder quadrature is used to monitor the speed and position of conveyor belts, robotic arms, and other rotary machinery. It provides feedback to the controller to ensure smooth and accurate motion, prevent collisions, and optimize production.
- Automotive: In the automotive industry, the incremental encoder quadrature is used to measure the speed and direction of the wheels, transmission shaft, and crankshaft rotation. It provides feedback to the engine control unit (ECU) for optimal fuel efficiency, emissions, and performance.
- Aerospace: In the aerospace industry, the incremental encoder quadrature is used in flight control systems, landing gears, and engines to measure the speed, position, and orientation of different parts. It is critical for ensuring the safety and reliability of aircraft during takeoff, flight, and landing.
- Healthcare: In the healthcare industry, the incremental encoder quadrature is used in medical devices, such as surgical robots, imaging equipment, and infusion pumps. It provides precise feedback for controlling the motion and positioning of the instruments, reducing the risk of errors or injuries.
In conclusion, the incremental encoder quadrature is an essential component of many industrial applications, providing accurate, reliable, and versatile motion control and feedback. With its high resolution, bi-directional output, real-time feedback, compact design, and durability, the incremental encoder quadrature is suitable for a wide range of industries, including industrial automation, automotive, aerospace, and healthcare.